Screen printing is a great way to add a personal touch to your clothing and accessories. However, it can be intimidating if you’re not familiar with the process. In this blog post, we will outline some tips for getting started with screen printing on supplies. From finding the right materials to getting started, these tips will equip you with everything you need.
Preparing the Supplies
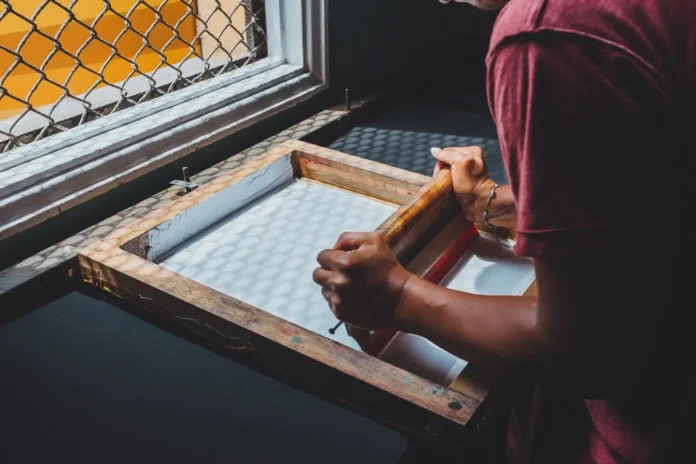
The most important thing is definitely some good quality screens. You’ll also need ink and paper, and sometimes other supplies like heat transfer material or adhesives. Here’s the most common screen printing supply list used in the process:
- Screens: These are the actual printing plates that your text or images will be printed on. They come in different sizes and shapes, so it’s important to find one that will fit your needs. There are also temporary screens available that can be used while your main screen is being cleaned or repaired.
- Ink: Screen printers use a variety of inks to create different colors and effects on the paper. Black, white, fluorescent green, and others are all common options. Be sure to have enough ink for whatever prints you plan on making!
- Paper: The paper is usually heavier than regular printer paper due to the ink demands of the process. You’ll need somewhere between 100 and 300 sheets for each print job, so make sure you have enough on hand! There’s also special matte paper designed for screen printing available, which can save you time and money in the long run.
- Heat Transfer Material: This is what makes your designs come to life on fabric or garments! It transfers the image from the screen onto the fabric or garment substrate, creating a final product that looks like it was printed with a regular printer.
- Adhesives: Screen printing often requires the use of adhesives to hold the ink and heat transfer material in place. There are a variety of different adhesives available, so be sure to pick the one that will work best for your project.
The Different Types of Ink
Screen printing is a popular way to create custom clothing, artwork, and other items. There are several different types of ink that can be used.
Pigment Inks: Pigment inks are the most common type of ink used in screen printing. They contain small particles of pigment that are dispersed in a solvent. When the solvent is applied to the fabric, the pigment particles attach themselves to the fabric fibers and create an image on the surface. Because pigment inks are so versatile, they can be used to create a wide variety of images and patterns.
One downside of pigment inks is that they tend to be less durable than other types of ink. They also require more attention when printing because they can easily become smeared or fused together if not handled correctly.
Water-Based Inks: Water-based inks are made up primarily of water and solvents, which allows them to be easy to apply but also makes them less stable than other types of inks. Because water-based inks don’t require any heat to print, they can be used for prints that need to be thermally stable (for example posters or banners). However, water-based inks aren’t as versatile as pigment inks because they don’t allow for as many different designs and patterns to be created.
Oil-Based Inks: Oil-based inks are some of the most versatile types of inks available. They can be used to create prints that are both thermally stable and durable. They also allow for a wider range of designs and patterns to be created than water-based inks. One downside of oil-based inks is that they can be difficult to apply accurately and can often require more time to print than other types of inks.
Tips to get you started
1. Choose the right printer
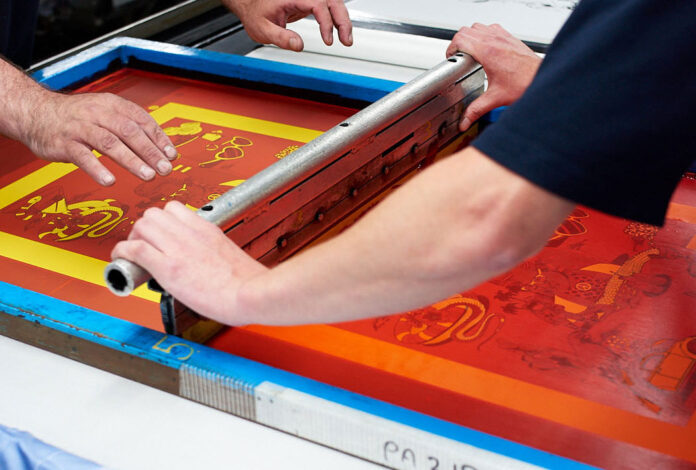
There are a few factors to consider when choosing a screen printer: price, size of print area, ink capacity, and output quality. Price is usually the most important factor; the lower the price, the higher the quality of the printer. The size of the print area is also important; you want a printer that has enough space so that you can print large prints without having to waste excessive amounts of paper. The ink capacity is important if you plan on printing multiple colors; some printers have larger ink capacities than others. The output quality is also important; you want your prints to look good and have accurate color reproduction.
2. Pre-plan your prints
Before starting any printmaking project, it’s helpful to plan what you want to print and where you want them placed on your garment or object. This will save time and ensure that your prints are placed where you intended them to be. You can use templates or free online tools like Google Sheets to make design software easily accessible from anywhere in the world!
3. Prepare your fabric correctly beforehand
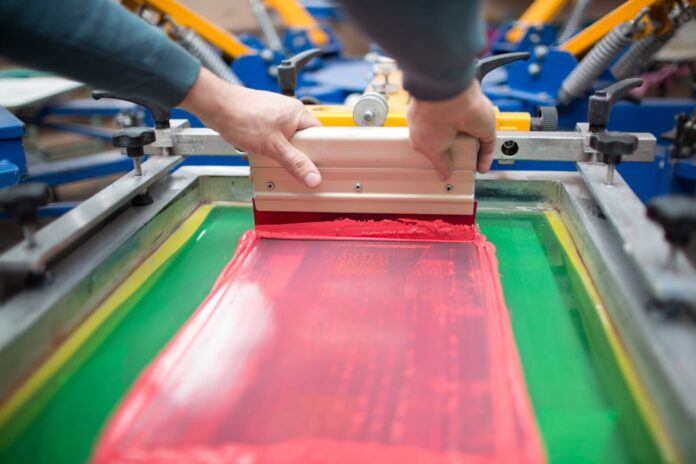
Make sure that your fabric is prepared properly before printing so that the ink doesn’t seep through and ruin your garment or object. Pre-wash your fabric if necessary, and then dry it completely before printing.
4. Use the right inks and settings for your fabric
Ink is the key to a successful print, so make sure to use the right inks and settings for your fabric. Inks can be classified as water-based or solvent-based. Water-based inks are less aggressive and are used on fabrics that don’t require a lot of ink coverage; they’re also less expensive than solvent-based inks. Solvent-based inks are more aggressive and are used on fabrics that need a lot of ink coverage; they’re also more expensive than water-based inks. When printing with solvent-based ink, make sure to use low settings on your printer because high settings will cause the ink to bleed through your fabric.
5. Test out your prints before you go live
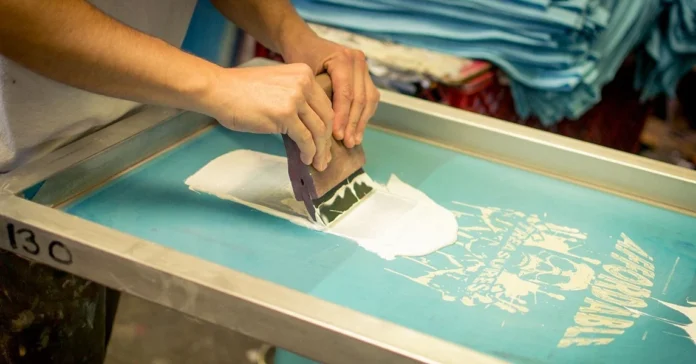
Before you go live with your prints, it’s important to test them out on a small piece of fabric first. This way, you can make any necessary adjustments before printing on a large scale.
Conclusion
Screen printing is a great way to create custom clothing and accessories. Hopefully, we’ve covered everything you need to know about the process, from the basic steps involved in setting up a print shop to more advanced techniques. We hope that this article has helped you understand the process better and given you some ideas on how to get started with screen printing.